Internal Training Academy Support
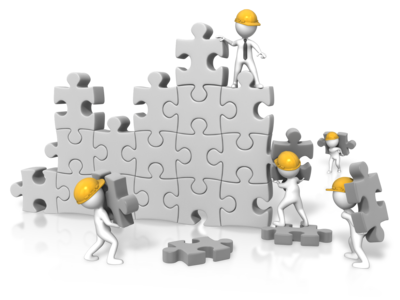
We provide bespoke programmes for internal training acadamies providing a mix of training workshops and coaching for front line teams, team leaders and business sponsors. The heart beat of the programme is a quarterly cycle of practical workplace projects that unlock the potential of individuals and support the delivery of business goals such as:
Leading Proactive Improvement
- Details
- Category: Internal Training Academy Support
Research into why some organisations succeed whilst other fail when applying Lean and TPM reveals the importance of Leaders investing time in removing barriers to future performance gains whilst simultaneously managing the challenges of day to day issues as they arise.
Those that do this well use the improvement activities to both improve performance and shape conversations that reinforce a culture of improvement pull.
This is a journey not a destination. Success depends on maintaining a creative pressure for change. Something that the LeanTPM Roadmap with its goal of continuous improvement in OEE was developed to support.
-
Overview
The importance of getting the balance right between the focus on technical improvement and people development is illustrated by the words of this CI manager after their programme began to deliver outstanding performance.
"In the beginning of the improvement journey, one of our top Production Managers thought, that 90 % of the reasons for ineffective use of the machinery was due to short term technical problems. Today he recognises that time invested in developing people to prevent problems is the route to high performance."
LEAN TPM ROADMAP
The Lean TPM road map, based on the practices of well respected and award winning organisations, guides the simultaneous development of senior management, front line leaders and front line teams to establish:
- A proactive improvement culture that drives significant year on year performance gains.
- Engagement with delivery of business improvement goals.
- Competency to apply the right blend of Lean and TPM tools to meet the challenge of each phase of the journey to industry leading performance.
A COMMITMENT TO IMPROVEMENT PULL
At the heart of that winning approach is a Leadership commitment to
- Deliver improvement pull by engaging the workforce with improvement as part of the daily routine,
- Rather than top down driven initiative push by management edict.
- The outcome is a work environment where people engage every day in removing waste and hidden losses by improving the effectiveness of working methods.
Using Cultural Change LeversThe strongest lever that leaders have to deliver lasting improvement are their conversations with peers and direct reports. The creation of a formal improvement agenda uses that lever to align cross functional outlook, encourage shared learning and drive engagement with a common set of improvement goals.
These are the building blocks for improvement pull.
Plan the plan workshops provide management and project teams with a forum to raise awareness, set priorities and align the Leadership agenda. Through these sessions Lead teams achieve consistent message/pressure for change and become coaches to raise the capability and level of engagement of their direct reports.
LeanTPM Planning the Plan facilitated working sessions cover:
- Improving Reliability and Resilience
- Performance Management
- Better projects faster
- Delivering gains from advanced technology
The outputs from these sessions include answers that matter about:
- Strengths and weaknesses compared to respected and award winning organisations.
- Potential improvement themes and priorities
- Next steps for senior management, functional heads, front line leaders and their teams.
That provides Leaders with a vehicle to:
- Raise awareness, win hearts and minds and get buy in to those new ideas.
- Improve insight into issue/opportunity causal factors and identify next steps.
- Surface barriers (real and imagined) overcome problems, refine ideas and progress them further.
- Guide the introduction of new working practices covering.
- Leadership and direction setting.
- Execution of routine activities to get better every day.
- Goals and metrics to measure progress and sustain the gains.
Stand on the Shoulders of GiantsThe next step to delivering lasting improvement is to understand the shop floor reality. Start with practical projects in a pilot area to learn how to remove barriers and build on good practices. Then roll out the lessons learned across the business.
The Lean TPM Roadmap is based on the improvement journeys of organisations who have achieved step out gains in performance through systematic improvement. Using those milestones (see below) to identify where you are on the journey and how to progress further is like standing on the shoulders of giants.
Phase 1 Improving reliability and resilience
Phase 2 Ratchet up performance
Progress through each phase involves different blends of Lean and TPM tools to meet their unique challenges.
- Phase 1 involves tools to deliver stable operation and prevent the causes of downtime,
- Phase 2 involves tools to optimise asset performance and remove the causes of defects.
A journey from taming technology to ratcheting up performance.
Rinse and RepeatAs each improvement milestone is approached, planning the plan activities confirm readiness to proceed and actions needed to progress further on the journey to industry leading performance.
This typically includes train the trainer and coach the coach activities to develop policy standards, raise capabilities, provide real time feedback and guidance on how to resolve implementation issues.
THE GAINS
Although their are financial gains throughout the journey, the biggest gains from the LeanTPM Roadmap are achieved by actions to:
- Develop high performance front line teams.
- Release management and specialist time from day to day operations.
- Focus that time and create new skills to enhance added value and advantage.
Contact us for more information about how our training courses and coaching pathways can support your improvement team development using our contact form
Leader Guide: Breaking Out of Reactive Maintenance
- Details
- Category: Internal Training Academy Support
The Break Out Road Map
The Break Out Roadmap is based on an analysis of successful countermeasures to breakdowns covering over 500 years of line running time. That analysis identifies 2 areas that contribute to 85% of the causes of breakdowns.
Fix these issues first to create the time and head space to progress from reactive to proactive maintenance.
Below is a summary of how to make that happen.
-
TPM Centre of Excellence Part 1
The breakout process involves stakeholders working together to surface and deal with the underpinning causes in a model area. This begins with the creation of a Centre of Excellence in a model area to:
- Develop an appreciation of the full range of issues to be addressed.
- Utilise the full knowledge and experience of the team to agree next steps
- Develop a deeper understanding of causal factors and collate lessons learned
- Test and refine potential solutions
- Implement and standardise new ways of working
- Lock in the gains.
The outcome is a deeper understanding of cause/effects and the development of countermeasures and standards which can then be transferred across the site.
Support Plan Structure
1: TAKE STOCK AND ENCOURAGE NEW THINKING.
- Readiness Review: Assess strengths, weaknesses, improvement potential and develop recommended next steps
- Plan the plan: Develop forward workplace learning projects
2: RAISE PERFORMANCE AND RELEASE POTENTIAL
- Training workshop: Asset Improvement Plan process to achieve standard speed
- Workplace Learning Project Scope:
- Define/confirm normal conditions and countermeasures to common problems
- Assess condition, identify and reduce accelerated wear
- Set and maintain basic equipment conditions
- Establish repair methods
- Organise routine production tasks
CHAPTER 3: BUILD CAPABILITY AND ENGAGEMENT
- Mid project review, policy development and forward planning
- Define critical control protocols
- Review/refine current control philosophy
- Standardise best practice routines.
4: DELIVER THE FULL POTENTIAL
- Capture lessons learned as Policy Standads and roll out to other areas.
Support Plan Example
Below is an example of DAK Academy support for practical improvement project around a troublesome asset. (Follow the links for more details of individual courses.)
A. Diagnostic Session:
Reliability for Manufacturing Leaders
Format: Remote/Online Session
This 2 hour on-line awareness workshop provides an insight into how award winning and well respected organisations are able to systematically deliver reliable, stable operations.
Learn how to counter the traditional pressures on output and break out of the reactive manufacturing environment where there is no time to deal with the root causes of unplanned downtime even when they are understood
B. Mobilisation Training Workshop:
Maintenance Planning, Scheduling and Work Control
Formats: In House training Workshop or Online
This training workshop provides a practical insight into best practice maintenance planning, scheduling and work control. That includes exercises to develop a customised pro-active maintenance planning approach as a driver for year on year improvement in maintenance effectiveness.
Learn how industry leading performers systematically progress from:
-
- Reactive ("fix-it-when-it-breaks") maintenance towards
- Predictive, productive asset management ("Stabilise and extend component life, predict when to fix-it-before-it-breaks and eliminate the causes of breakdowns").
C. Remote Implementation Support:
Drafting and Reviewing Asset Care Plans
Format: Remote/Online Training
This course provides participants with an understanding of best practice asset care principles and practical advice on how to achieve high levels of reliability. That includes the review of existing practices to understand and deal with the underpinning causes of problem hot spots.
Click on link for more information on Learning to improve Reliability
Take ControlAround half of breakdowns are due to lack of knowledge and skills of front line users.
Start with the work on problem assets to restore asset basic conditions and create basic condition standards. Use the process to develop front line team and team leader understanding and their capability to:
- Maintain basic conditions
- Collaborate with maintenance to
- Create a stable, organised approach to asset care.
- Develop trouble shooting algorithms for problem hot spots to systematically improve insight into cause effect mechanisms and improve inspection routines.
- Refine awareness and training plans to
- Embed visual standards within work routines so that they are easy to do right, difficult to do wrong and simple to learn
- Overcome knowledge and skill gaps.
- Assess competencies and assure high levels of cross shift compliance
The gains from dealing with these weaknesses are significant because applied to problem assets, they can become standards which are used to assure high levels of reliability for all assets.
The outcome includes the release of specialist and management time to focus on higher value activities.
Contact us for more information or to arrange a call to discuss how we can support your Breakout Reliability programme.
Get BetterBusiness Leader Development Modules
Who
Task
Learning Plan Content
Business Sponsor, Support specialists, CI Manager
Design, mobilise and manage the breakout programme
Release and share knowledge and latent capability.
Improvement principles, gap analysis, prioritisation and goal alignment, top down planning, organisation and control.
Departmental Leader Development Modules
Who
Task
Learning Plan Content
Departmental Head and Team Leaders
Communicate the cause/effect linkages between effective maintenance and total costs
Set and assess equipment condition standards
Implementation roles and implementation route map and coaching to establish better working practices.
Planners and Administrators
Integrate the improvement activities as part of the routine work plan
Asset plan development, improvement glide path definition, resource scheduling, tracking and capture of lessons learned.
Engineering specialists and Trainers
Define training needs by skill category (Not by asset)
Standardise and systemise best practice to make it easy to do right, difficult to do wrong and simple to learn.
Front Line Team Development Modules
Leader Guide: Scaling Up For Growth
- Details
- Category: Internal Training Academy Support
The Scale Up Road Map
This second support programme builds on the progress made to date through the Breakout Road map to lock in the gains and support task transfer. That releases specialist resource and management time from dealing with day to day issues to carry out higher value adding activities.
That is equivelent to meeting the challenge of draining the swamp whilst fending off the crocodiles.
Even where the capacity gains cannot be easily converted into output, these countermeasures reduce the risk of human error and levels of quality defects. They also speed up skill development and improve workforce flexibility.
-
TPM Centre of Excellence Part 2
The Scale up Roadmap involves stakeholders working together to surface and deal with the underpinning causes of capacity constraints. That enhances the Centre of Excellence capabilities by making progress from ad hoc problem solving to focussed improvement. Find out more here.
That includes better use of data to develop a deeper understanding of cause/effects and to develop competencies to support improved flow and capacity.
Support Plan Structure
1: TAKE STOCK AND ENCOURAGING NEW THINKING.
- Readiness Review: Assess strengths, weaknesses, improvement potential and develop recommended next steps
- Plan the plan: Develop forward workplace learning projects
2: RAISE PERFORMANCE AND RELEASE POTENTIAL
- Training Workshop: The glide path to optimum conditions
- Core Team Sessions: Identify problem hot spots
- Review/refine asset care
- Review/refine operating standards
- Improve design weaknesses
- Prevent mis operation
- Prevent repair errors
3: BUILD CAPABILITY AND ENGAGEMENT
- Mid project review, policy development and forward planning
- Standardise core skills for normal conditions
- Reduce unplanned adjustments
- Systemise planned adjustments
4: DELIVER THE FULL POTENTIAL
- Capture lessons learned as Policy Standads and roll out to other areas.
Support Plan Example
Below is an example of how to develop capabilities to ratchet up effectiveness using a practical improvement project around a key asset. (Follow the links for more details of individual courses.)
A. Diagnostic and Plan the Plan Session:
Reliability for Manufacturing Leaders
This 2 hour on-line awareness workshop provides an insight into how award winning and well respected organisations are able to systematically deliver reliable, stable operations.
Learn how to counter the traditional pressures on output and break out of the reactive manufacturing environment where there is no time to deal with the root causes of unplanned downtime even when they are understood
B. Mobilisation Training Workshops:
TPM Best Practice Implementation
Format: 3 Day hands on training workshop
Learn how to implement Total Productive Manufacturing principles and techniques to release the full potential of your people, procedures and work processes.
Turn theory into practice during the workshop by applying theory to assets on the factory floor using a comprehensive TPM application workbook.
C. Implementation Support:
Format: Online 4 sessions
First Line and Mini Business Leaders are at the heart of any organisations ability to deliver value to customers. They are the ones who can make an organisation run like clockwork. As customer expectations ratchet up and the pace of technology accelerates, their role is evolving. This training workshop will provide participants with a road map to equip First Line leaders with the knowledge and skills to drive practical changes through their teams.
Front Line Skill Development Best Practice
Format: 2 Day in house training workshop
The course content covers best practices for
- Role and task design
- Including the use of standards to accelerate learning
- Balancing team skill profiles
- Including issue response and resolution
- Asset and individual learning plans
- Training and compliance feedback
- Including methods improvement and standardisation
- Work instruction ownership and review
The course includes a systematic review of existing processes and work routines to surface barriers and identify actions to resolve them.
Take ControlThe scale up road map sets out the steps to standardise work routines and speed up skill development processes through actions to:
- Simplify critical and complex processes so that they are easy to do right, difficult to do wrong and simple to learn.
- Standardise core tasks to improve workforce flexibility and use of skills.
- Make normal conditions visible at a glance to improve early problem detection
That is underpinned by the development of effective shop floor processes and Front Line Leader skill skills to engage front line teams with practical actions to create:
1. A Plan for Every Asset (PFEA) to support the continuous update of working methods, standard practices and learning plans so that changes are controlled and work standards are maintained.
2. A Standardisation process covering Learning plans and pathways to structure the building blocks of capability development, employee engagement and high performance teamwork.
3. Local Area performance management processes that drive improvement in work practices, standards and skills as part of the day to day routine.
4. A Focussed Improvement glide path and tactics to systematically raise effectiveness.
Contact us for more information or to arrange a call to discuss how we can support your Scale Up Road Map programme.
Get BetterBusiness Leader Development Modules
Who
Task
Training Content
Business Sponsor, Support specialists, CI Manager
Make continuous improvement a part of everyone’s day job.
Set improvement challenges to trigger new thinking about business improvement priorities.
Scale up road map milestones, Gap analysis and Improvement policy deployment.
Departmental Leader Development Modules
Who
Task
Training Content
Departmental Head
Value hidden losses and wastes in financial terms Coach and mentor as part of the daily management process.
Implementation roles and implementation route map and coaching to establish better working practices.
Team Leaders
Visual management standards for flow coordination and adherence to best practice.
Front line skill development process covering task design, standardisation, learning plans and compliance management.
Engineering specialists and Trainers
How to identify technology issues and their cause/effect mechanisms.
Personal planning, mapping action plans, managing improvement activities and conditioning new working practices.
Planners and Administrators
Integrate the skill development activities as part of the routine work plan.
Setting team goals, evaluating progress against planned outcomes.
Front Line Team Development Modules
Leader Guide: Reducing Minor Stops and Defects
- Details
- Category: Internal Training Academy Support
Beyond Zero Breakdowns
Even with stable operation, it is not uncommon for jams, fallen bottles and electrical trips to reduce the Mean Time Between Intervention (MTBI) for production operators to minutes. Each stop reduces capacity, adds to energy costs and increases the risk of human error and quality defects.
By comparison, leading organisations have mean time between intervention measured in hours if not shifts. In addition to freeing up time, that extends component life, improves material yield, reduces quality defects and saves energy. That also improves process resilience and the ability to flex output to match customer demand.
-
TPM Centre of Excellence Part 3
The causes of Idling and minor stops are easily overlooked when production plans are based on asset demonstrated capability rather than Asset capability.
As long as the plan is achieved, there is little pressure to do more but minor stops are major contributors to the instability that results in quality defects.
This support plan enhances TPM Centre of Excellence capabilities to systematically remove the causes of unplanned interventions. The same tool set can then be applied to reduce levels of planned intervention and progress towards no touch production.
Support Plan Structure
1: Take stock and encourage new thinking.
- Readiness Review: Assess strengths, weaknesses, improvement potential and develop recommended next steps
- Plan the plan: Develop forward workplace learning projects
2: Raise performance and release potential
- Training Workshop: The improvement glide path for minor defects
- Core team sessions: Categorise defects and causal factors
- Review equipment capability
- Enhance installation precision
- Improve ease of use and maintenance
- Enhance precision of adjustments, jigs and fixtures
- Enhance set up precision.
3: Build capability and engagement
- Mid project review, policy development and forward planning
- Prioritise minor defect hot spots
- Establish control points and methods for defect control
- Extend Mean Time Between Intervention
- Stabilise and extend component life
- Increase standard speed.
4: Deliver the full potential
- Capture lessons learned as Policy Standads and roll out to other areas
Support Plan Example
Below is an example of a support plan to develop capabilities, guide and facilitate the systematic reduction of defects and minor stops (Follow the links for more details)
A. Diagnostic Session:
Daily Management Best Practice for Manufacturing Leaders
Format: 2 hour online
This short on line awareness workshop is designed to both raise awareness and assess current practices against benchmarks for the daily management best practices used by award winning and well respected organisations. These processes are at the heart of the capability to ratchet up performance through actions to simultaneously:
- Build shift/area team capabilities
- Develop insight and learning to underpin year on year improvement in effectiveness.
- Raise operational resilience and release time to proactively adapt to changes in new products, technology and statutory legislation
B. Mobilisation Training:
The outputs from the awareness session include an action plan which is likely to include the mobilisation of a cross functional team. Below are training sessions which are designed to facilitate the launch of an improvement projects and workplace learning cycles.
Format 3 Day training workshop or individual training modules over 4 to 12 weeks.
This is a course designed to support those tasked with achieving the challenging but achievable TPM goal of zero breakdowns.
At the heart of the TPM process are practical, cross functional team processes that systematically improve Overall Equipment Effectiveness as part of the daily routine.
This provides local and senior leadership with the levers to engage production and engineering personnel with a shared improvement agenda to ratchet up performance.
Format: 3 Day training workshop or individual training modules over 4 to 12 weeks.
Learn how apply the Lean Maintenance to build on existing good practices and improve:
- Lean Asset maintenance execution through standard work that:
- Remove the causes of accelerated wear and human error.
- Improves working methods, speeds up skill development and simplifies spares management.
- Lean Execution to support
- Process optimisation
- Workflow Management,
- Problem Prevention toolsets
- Lean Management to
- Stabilise and extend component life
- Improve use of skills and flexibility
- Enhance data analysis and CMMS added value
- Project manage shutdowns or the introduction of new equipment, systems, products and services.
The content includes lessons from well known and award winning organisations to explain how engaging Maintenance within a Lean programme can deliver as much as 50% more in terms of year on year gains
C. Implementation Support:
Developing First Line Leadership Skills
Format: Online 4 sessions
First Line and Mini Business Leaders are at the heart of any organisations ability to deliver value to customers. They are the ones who can make an organisation run like clockwork. As customer expectations ratchet up and the pace of technology accelerates, their role is evolving. This training workshop will provide participants with a road map to equip First Line leaders with the knowledge and skills to drive practical changes through their teams.
Front Line Skill Development Best Practice
Format: 2 Day in house training workshop and follow up coaching
The course content covers best practices for
- Role and task design
- Including the use of standards to accelerate learning
- Balancing team skill profiles
- Including issue response and resolution
- Asset and individual learning plans
- Training and compliance feedback
- Including methods improvement and standardisation
- Work instruction ownership and review
The course includes a systematic review of existing processes and work routines to surface barriers and identify actions to resolve them.
Take ControlMinor stops can become accepted as inevitable yet the most common reasons why they are not dealt with can be described as "gaps in the fabric of management" relating to
- What to do when things go wrong: When complex problems such as minor stops are encountered, with the pressure of production output, the simplest thing to do is restart the machine. As the root causes are never dealt with they will resurface in the future.
- How to manage change: That covers processes used to introduce new ideas and priming the ideas pump to make people curious about what could be done to improve the current state.
- How to encourage behaviours that:
- Reinforce standards of work and highlight capability gaps
- Make it easy for front line roles to highlight and resolve missing or complex work routines.
- Develop capability, build on new ideas and share lessons learned.
The gains from fixing these "gaps in the fabric of management" are significant but in most cases, those gaps never feature in performance reports.
In most cases the countermeasures are low cost or even no cost.
Get Better
Leader Guide: Delivering Step Out Performance
- Details
- Category: Internal Training Academy Support
Releasing New Value from Operations
This fourth support programme develops the capability to sustain operational effectiveness whilst introducing improved products and services to set the customer agenda and deliver growth.
That can achieve step out gains where there is close collaboration between commercial, operations and technology functions.
This close collaboration supports horizontal learning, primes the innovation pump and speeds up the conversion of value proposition ideas into higher added value products and services.
As part of the delivery of new product and service offerings the improvement process releases new value from operations such as:
- Increased Precision, higher material yield and lower levels of quality defects,
- Improved flow of value and reduced customer lead times,
- High productivity, flexibility and responsiveness to shifts in demand.
-
TPM Centre of Excellence Part 4
This support plan extends the scope of TPM Centre of Excellence capabilities to cover New Product Introduction which often involves the delivery of capital investment projects. That includes the application of Early Equipment Management (EEM) tools to:
- Surface latent project problems early in the project timeline so that they can be dealt with when they are easier to resolve.
- Highlight opportunities to enhance project value and achieve higher levels of return on investment.
- Coordinate the glide path to flawless operation from day one and beyond.
Support Plan Structure
1: TAKE STOCK AND ENCOURAGING NEW THINKING.
- Readiness Review: Assess strengths, weaknesses, improvement potential and develop recommended next steps
- Plan the plan: Develop forward workplace learning projects
2: RAISE PERFORMANCE AND RELEASE POTENTIAL
- Training Workshop: Project Management Routemap: Early Equipment Management Planning organisation and control.
- Core team activities:
- Get the Right Design: Operations Review, Module definition, Specification development.
- Get the Design Right: Vendor Evaluation, Detailed Design and Project Glide Path design.
3: BUILD CAPABILITY AND ENGAGEMENT
- Mid project review, policy development and forward planning
- Managing Project Delivery: Factory Readiness Plans for Installation, commissioning and Operational ramp up.
- Managing Operational change: Developing capability for new assets and systems.
4: DELIVER THE FULL POTENTIAL
- Capture lessons learned as Policy Standards and roll out to other areas.
Contact us for more information or to arrange a call to discuss how we can support your programme to achieve Step Out performance levels.
Take ControlThe Step Out support plans below provide cross functional teams with working sessions and coaching to guide the team to:
- Develop a common understanding of the issues to be addressed.
- Utilise the full knowledge and experience of the team to agree next steps.
- Develop a deeper understanding of causal factors and collate lessons learned.
- Test and refine potential solutions.
- Implement and standardise new ways of working.
- Lock in the gains.
Sample Support Programme
The format and content of working sessions are customised to meet specific step out goals and industry requirements. Below is an example of a sample support programme with links to stand alone courses to provide further details.
A. Diagnostic Session:
Delivering gains from advanced technology
Format: half day on line
This half day on line session is designed to raise awareness of the evolving best practice road map and identify where advanced technology can deliver step out gains. That includes
- The building blocks of success.
- How to avoid the common implementation pitfalls that result in pilot purgatory.
- How to deliver gains from this disruptive technology.
B. Mobilisation Training Workshops:
Manufacturing Project Management,
Format: 3 day in house training
Successful delivery of Manufacturing Projects depends as much on engaging stakeholders with new thinking and knowledge capture as it does on classic project management tools.
This course covers how to do that to produce winning specifications and the realistic and achievable plans to deliver them.
Learn how to avoid common manufacturing project pitfalls, deliver better value and achieve higher return on investment. Be able to develop a robust project management skill set.
C. Implementation Support:
Format: Coaching Plans for Key Stakeholder Roles
EEM extends the traditional project focus of delivering a new asset or engineering platform to that of delivering Operational Excellence. The difference is the humanisation of projects to incorporate not just what will be done but how it is done. This is characterised by increased collaboration between commercial, operations and technical personnel at all project steps.
Get BetterBusiness Leader Development Modules
Who
Task
Learning Plan Content
Business Sponsor
Evaluate new ideas and refine through practical application.
Develop productive alliance relationships to create new value whilst protecting IP.
Improvement Master Plan development, People Centric Leadership.
CI Manager
Policy Deployment, Performance Management and Audit/Coaching.
Loss tree analysis and improvement glide path modelling.
Process and workflow enhancement to remove process pain points and generate new value from operational flexibility and resilience.
Departmental Leader Development Modules
Who
Task
Learning Plan Content
Departmental Head
Analyse the customer total cost of ownership and sponsor cross company actions to develop customer value adding features.
Implementation roles and implementation route map and coaching to establish better working practices.
Team Leaders
Coach front line teams to develop self management capabilities and collective control of routine activities.
High performance teamwork steps, understanding behaviours.
Planners
Integrate the improvement activities as part of the routine work plan.
Setting team goals, evaluating progress against planned outcomes.
Support specialists
Collaborate with commercial and technical personnel to deliver better than new performance and capital projects that achieve flawless operation from day 1.
See below:
C1
Investigate processing/ mechanism theories.
Process/Chemistry foundations to assess phenomena in physical terms.
C2
Advanced analysis tools.
Increase precision of analysis and/or measurement. Incorporates P-M analysis and 6 sigma tools and techniques.
C3
Experiment to confirm phenomena, resolve causes of latent defects.
Identify feature/process/ parameter/control point causal links and optimisation tactics.
Front Line Team Development Modules
Leader Guide: Delivering Better Projects Faster
- Details
- Category: Internal Training Academy Support
This Leader Guide sets out training and coaching plans to develop the capabilities of those in Project Team Member, Project Leader and Project Governance roles so that they are able to deliver better projects faster.
That is achieved through practical working sessions alongside live project programmes providing timely input and guidance on how to:
- Create superior specifications,
- Discover latent problems early when they are cheaper to fix,
- Manage and prevent project risks,
- Develop the insight to deliver additional project value.
-
What Project Stakeholders Need To Learn
Project Stakeholders without previous experience of projects need to learn how to:
- Develop realistic and achievable project scopes.
- Collate and share knowledge about problems which may not be fully understood.
- Define tests to validate/commission new assets or processes which have yet to be selected.
- Collaborate with outside companies to assess promising solutions
- Establish new working relationships, challenge limiting behaviours and provide a forum for learning about novel solutions to the organisation
- Coach direct reports past the barriers to higher levels of performance.
- Develop the full potential of newly formed operational teams.
Even where some project team members are experienced, there is value in including training in the form of working sessions at key project steps to share ideas, align priorities and identify opportunities to enhance project value added.
Contact us for more information about how working sessions help project stakeholders to make better choices at each project milestone
Developing Project Team CapabilitiesFacilitated working sessions provide a combination of training in best practices and practical application support to guide project stakeholder actions to:
- Develop a common understanding of the issues to be addressed.
- Utilise the full knowledge and experience of the team to agree next steps
- Develop a deeper understanding of causal factors and collate lessons learned
- Test and refine potential solutions
- Implement new ways of working.
Training and Coaching Plan Example
The programme below illustrates how facilitated working sessions develop project stakeholder capability to understand their role and develop the insight to deliver superior results at each step of the project process from concept to beneficial operation.
Diagnostic session:
Early Equipment Management for Manufacturing Leaders
Format: half day on line
This working session provides a "how to" guide to avoiding common project pitfalls and drive up additional project value.
That includes an explanation of Early Equipment Management (EEM) best practice principles and practical activities to enhance the current draft project plan. The final session involves the development of 90 day action plans to apply the lessons learned during the session.
Mobilisation training workshops:
Manufacturing Project Management
Format: 3 day in house training workshop
Successful delivery of Manufacturing Projects depends as much on engaging stakeholders with new thinking and knowledge capture as it does on classic project management tools.
This course covers how to do that to produce winning specifications and the realistic and achievable plans to deliver them.
Learn how to avoid common manufacturing project pitfalls, deliver better value and achieve higher return on investment. Be able to develop a robust project management skill set.
Implementation Support:
Format: In house and remote coaching at project stage gates
EEM extends the traditional project focus of delivering a new asset or engineering platform to that of delivering Operational Excellence. The difference is the humanisation of projects to incorporate not just what will be done but how it is done. This is characterised by increased collaboration between commercial, operations and technical personnel at all project steps.
Project Skills PassportProject Skills Passports set out the core, intermediate and specialist competencies for each project role. This is used to record demonstrated capabilities as each level of competence is achieved. The outcome is the systematic development of internal capabilities to deliver better projects faster.
Table 1 contains foundation topics to develop a shared project outlook across all roles. This training also helps to surface gaps in underpinning systems and processes so that they can be refined to secure the achievement of flawless operation from day 1.
Table 1: Foundation learning for all Project Roles
Title
Topic
Content
Level
Training Content
The Project Route
The decisions at each stage, the processes to be sure we don't miss things and the processes to prevent issues from being transferred to the next step
Milestone plan, tasks, RACI
Core
Project Road Map
Get the right design
Concept and High Level Design tasks.
Operations “Day in the Life of” design review.
Core
Developing the right approach
Get the design right
Detailed Design and Pre installation tasks
Witnessed inspection and designing the training cascade
Core
Design a robust solution
Managing Project Delivery
Install and commission
Factory Readiness Plans
Delivering the training cascade witnessed inspection
Core
Refine the new operation
Managing Operations changes
Developing capability
Skill development, standardisation and compliance.
Intermediate
Detailed Design
Project Mindset
Team leadership, Collaboration and Decision making when data is scarce.
Facilitation principles and techniques
Specialist
Concept. High Level Design, Pre-Installation Planning
The second table covers training topics relating to the project sponsor role of setting design and performance standards. This is a leadership role responsible for communicating with and guiding project leaders and team member decisions so that they deliver design and performance management goals to meet future business needs.
Table 2 Learning Pathways for Project Governance Roles
Title
Topic
Content
Level
Training Module
Defining equipment performance drivers
Understanding functionality, skill gaps, hidden losses and countermeasures, understanding life cycle cost drivers
Module definition, Criticality assessment,
OEE, Hidden Losses, Flow, setting targets
Module review understanding losses defining commissioning criteria
Core
Enhancing Project Value
Using standards and checklists
Setting Design Standards to guide optioneering
Using design standards to guide decisions when defining options and working with vendors
Core
Designing robust solutions
Developing operational standards and checklists
How to guide design decisions and project management delivery options
Day in the Life of review and design goals. Develop acceptable and optimum criteria
Intermediate
Pre Installation step
LCC cost model
Use of Life Cycle Cost models to understand cost drivers and support option evaluation.
Capital and operational cost streams with parameters for throughput, product mix and effectiveness levels.
Specialist
Planning Steps
Table 3 Learning Pathways for Project Teams and Operational Leaders
The final learning plan covers topics for project team members. This initially refers to a core project team involved in the concept and high level design steps. This team will expand to include operational leaders and front line teams as the project progresses towards day one operation.
Title
Topic
Content
Level
Training Module
Developing project plans
Milestone planning, setting exit criteria to define project quality plans.
Quality plan timing and completion of internal documentation e.g. capex process
Core
Project Road Map
Using project quality plans
Carrying out witnessed inspection
Test criteria
Core
Develop the right approach
Project links with other business processes
Capex, PMS, QA, Documentation, Risk management, Legislation
Capital project underpinning systems and interfaces.
Core
Refine the new operation
Developing collaborative plans
Action mapping for project scope definition and vendor induction
Facilitating cross company events to agree a consolidated project strategy and supporting work streams
Intermediate
Detailed Design
Project governance
How to design, mobilise and support outstanding capital project teams
Project Roles, setting targets. RACI
Steps and stage gates
Specialist
Concept
The final learning plan covers topics for project team members. This initially refers to a core project team involved in the concept and high level design steps. This team will expand in the project progresses through the project delivery steps when more detail is added to design and deliver factory readiness plans.
Factory Readiness for New Technology Projects
- Details
- Category: Internal Training Academy Support
Digitisation combines the improved connectivity of Advanced Technology with the use of a digital backbone of micro systems and analysis tools to release the barriers created by legacy systems and deliver step out performance gains.
Delivering those gains involves working with users to assess current end to end workflow, align project team outlook about gaps and mobilise practical projects to both deal with the gaps and raise capabilities. Here are the lessons from those who have learned how to do that well.
-
Meeting The Legacy Process Challenge
Historical business processes developed during times of growth or acquisition can result in a legacy of multiple systems and procedures that meet the needs of individual functions but which present barriers to workflow. As wasteful are integrated systems where users create spreadsheets to manipulate data outside of the main system to provide them with the information they need to be able to function.
Advanced technology delivers improved connectivity which can remove these barriers. In addition, because the information is in the digital domain, this can be utilise machine learning and data models to aid decision making and provide guidance.
Digitisation, combines enhanced connectivity with the use of digital decision aids to compress the "end to end" Plan, Source, Make Deliver value adding process. An approach that delivers a step change in Quality, Cost and Delivery performance.
Those that have learned how to harness the potential of Digitisation have found that success depends on the engagement of users in systematic improvement. This is a journey rather than a destination.
To deliver these gains, the implementation project involves users in working with the live system to refine work routines and systematically enhance the end to end process.
That involves creating project teams with the goal of making a step change in the performance of business critical processes.
Digitisation activities can stall by focusing on things that have little consequence to business objectives. Avoid the temptation to start with ancillary processes.
Dealing with Legacy Systems
1. Understand the end to end process and identify the pain points to delivering step out performance.
2. Get user departments together, provide training in digitisation tools and encourage them to be curious about what could be, how to overcome pain points and priorities for improvement.
3. Starting with a model area, develop or identify web based microsystems that link up priority systems to create a digital backbone which can be used remove pain points.
4. Understand the customer and what they value. Define what is important to them and ensure that these attributes drive the design of the new process.
5. Define roles to fit the process: Avoid the classic approach to re-organisation which starts from the perspective of individual roles and personnel. The process purpose and value added need to be the prime considerations.
6. Track performance of the live system and review/refine work routines to lock in the gains.
7. Rinse and repeat
Contact us to find out more about how we can help to engage the workforce with delivering gains from advanced technology.
Working Session: Accessing Advanced Technology GainsWithin any medium to large sized organisation there will be a myriad of processes with interdependencies that are not always clear. That makes the delivery of a step change in performance both difficult and risky unless those currently doing the work are engaged with the improvement process.
The content of this half day session is structured to support discussion around the current approach to advanced technology, potential gains and how to access those gains. That includes the completion of a diagnostic review framework to identify areas of strengths and weaknesses and support the development of action plans covering 5 year, 12 month and 90 day time horizons.
This can be customised to support a range of activities including strategic review, programme design, or project team mobilisation.