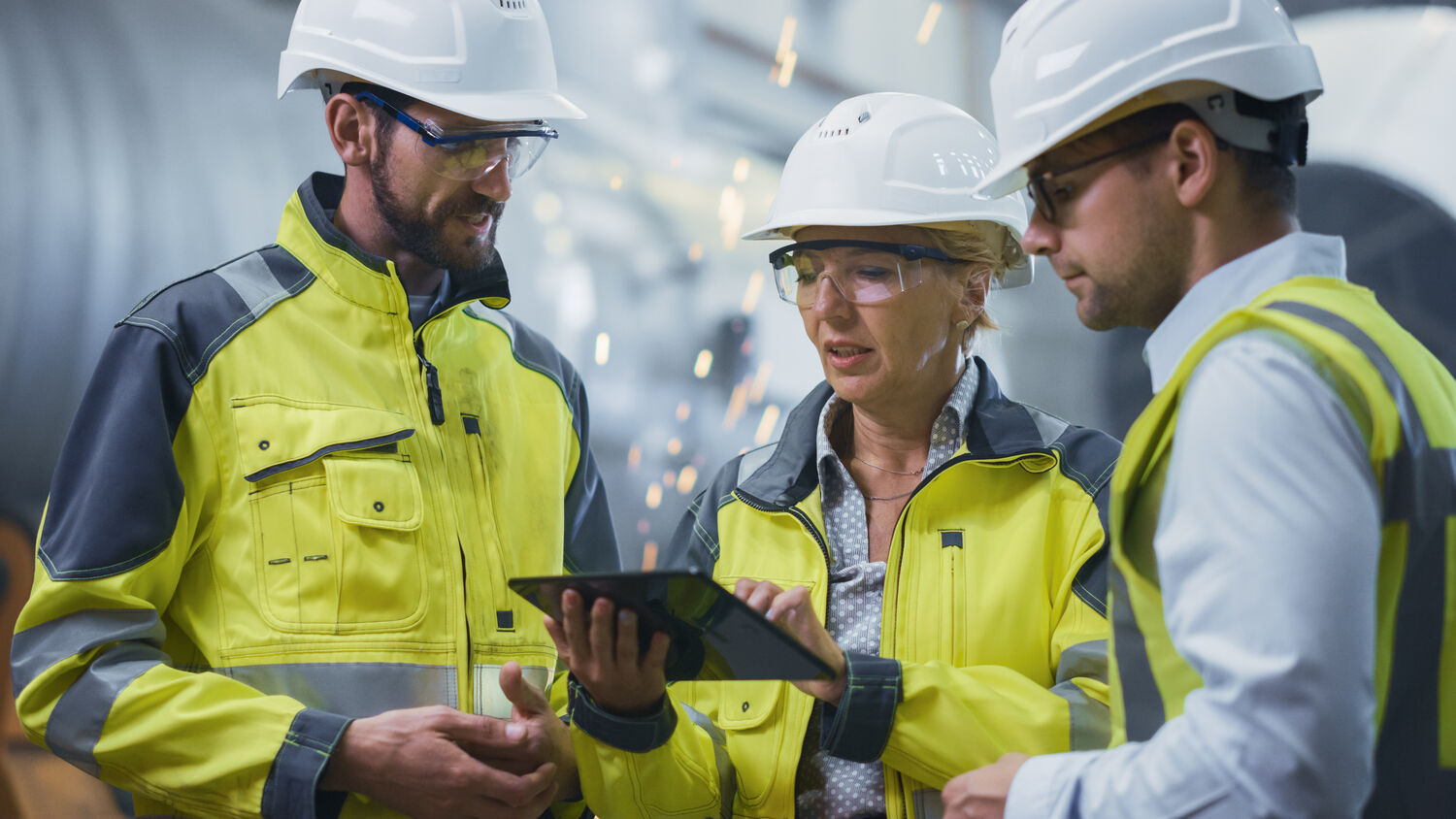
- Dates: 2 Hour session
- Location: Live On Line
- Cost: £250 plus VAT
- Details
- Parent Category: Courses
- Category: Improving Reliability and Resilience
This short 2 hour on-line awareness workshop is designed for between 2 and 8 people and can be customised to support manufacturing leader development, reliability status review, improvement planning or project team mobilisation.
The content provides an insight into how award winning and well respected organisations apply Lean Maintenance principles to deliver Zero Breakdowns and engage front line production and maintenance teams with ratcheting up performance.
Learn how to break out of the reactive manufacturing environment where there is no time to deal with the root causes of unplanned downtime even when they are understood.
Much of the academic literature around reliability focusses on failure curves yet the majority of calls for immediate maintenance support are not to respond to failed components. Most unplanned interventions are in response to issues such as jams, blockages, electrical trips or a build up of contamination. That type of problem also soaks up a significant amount of operator time. It is not uncommon for the Mean Time Between Intervention (MTBI) for a production line to be measured in minutes.
By comparison, by adopting Lean Maintenance principles, leading organisations achieve mean time between intervention measured in hours if not shifts.
In addition to gains in capacity and lower maintenance costs, this also improves process yeild, and reduces energy costs.