Blog
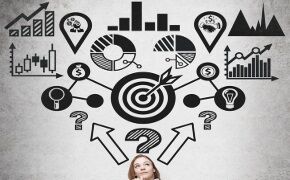
The articles below explain how to overcome common barriers to improvement and how industry leaders sustain the gains where others are not able to.
This is based on our work with well-known and award winning organisations. There is much to learn from them. If there are any topics you would like is to add, please get in touch.
For more detailed articles check out our DAK Academy website guide which contains links to videos, articles and downloads.
Delivering Technology Project Added Value
- Details
- Category: Blog
A significant proportion of the gains from smart technology are delivered by using better data or connectivity to fix gaps or weaknesses in management processes. In some cases it can also be the trigger to change the business model to access new markets and added value.
That is changing how investment projects are justified, how returns on investment are generated and how projects are managed. This is an approach which engages stakeholders with decisions about design, project delivery, risk management and the generation of additional project added value.
An approach that also delivers streamlined project delivery, risk reduction and the foundations to achieve flawless operations from day one.
Here are some examples of what can be achieved and how to replicate that success.
Adaptive Project Management and why you need it
- Details
- Category: Blog
For the traditional waterfall approach to work, all options must be identified and evaluated at the Define phase so that the Design and Refine phases are simply completing what has already been decided. In reality, this is seldom achievable without compromising cost, timescales and/or performance.
Although originally developed for IT applications, Adaptive Project Management can also be used for manufacturing projects. The gains include the flexibility to refine ideas and enhance project added value as part of the project brief. It also generates higher levels of user engagement which reduces risk and shortens timelines to beneficial operation.
Measuring Performance and Cultural Drivers
- Details
- Category: Blog
The saying goes "A Volunteer is worth 10 pressed men", a sentiment that most would agree with. In the past it hasn't been easy to measure the impact that motivation and engagement has on Quality, Cost and Delivery performance yet this is a big differentiator between poor and exemplar performers.
What is missing is a measure of what is known in TPM as "Normal Conditions". Normal condition indicators are what experienced shop floor personnel and leaders rely on to identify that a process is working well and where to intervene if it is not. How do they do that?
When Data Theory and Practice Don't Match
- Details
- Category: Blog
In theory prioritising issues is simple. Use a pareto to identify the asset with the most problems and work in that.
Unfortunately, it isn't as simple as that. The fault pareto analysis below showing the outputs from a shop floor data capture system, seems to indicate the main culprit to work on but this analysis isn't providing the full picture.
Creating a Smart Technology Transition Cadence
- Details
- Category: Blog
The fundamentals of how to ratchet up manufacturing effectiveness haven't changed. It's still a voyage of discovery with front line workers in the engine room. What has changed is a greater availability of real time data which enables better quality feedback and closer collaboration between production, maintenance and support functions.
Turning that potential into business gains is the equivalent of switching from letter post to emails or newspapers to smartphone news apps where the need for the post room or trip to the newsagent has disappeared. Something that requires collective leadership and a managed transition.
The starting point is to bring together the right people in a working session to understand the current reality, confirm priorities and develop realistic and achievable actions plans. Here is how Digital Accelerator Training workshops support that process,
Making Better Use of Skills
- Details
- Category: Blog
The site had begun to put into place actions to counter the impact of the future retirement of experienced maintenance personnel but recognised that this issue was a symptom of weaknesses in other areas. For example although they were making good progress with Lean and TPM they needed to improve results at tier 1 level. In addition they had been working on use of mobile devices, improving data historian, and condition monitoring but needed to improve how data was used to support day to day decisions.
We helped this organisation to build on existing good practices using our Lean Maintenance diagnostic model to assess their current status and identify next steps. Here is how we did that.
Leading Smart Technology Projects
- Details
- Category: Blog
Delivering gains from physical Smart Technology assets such as Robots, Cobots or 3D printing will involve linking up with and adapting existing systems, processes and ways of working. As a result, the implementation of Smart Technology projects involves the evolution of the current management ecosystem to adapt to the new technology.
Furthermore, the lack of this type of holistic approach is a common cause of failed Smart Technology applications.
Why is that?
Problem Detection and the Journey to Excellence
- Details
- Category: Blog
Being able to spot the tell tale signs that something has changed and acting on it is a key enabler of the journey to excellence.
Not only is this the capability to trigger actions that deal with issues before they become a problem it is also at the heart of learning about causal links to that support progress to process optimisation.
What does it take to make that happen?
What TPM Practitioners Can Learn From Top Gun
- Details
- Category: Blog
Aircraft Pilots are trained using key words to hone their instincts to apply a concept known as Threat and Error Management (TEM) to avoid "common threats, errors and undesired states" The concept of "Normal Conditions" in Manufacturing Operations adopts a similar approach to deal with the causes of human error which typically contributes to around 50% of recurring problems and unplanned stoppages.
Developing Improvement Leader Competence
- Details
- Category: Blog
A Development Plan for CI Facilitators
As organisations improve performance, the nature of the improvement journey changes.
For example, as organisations develop the ability to reduce unplanned stops, the role of those involved in shop floor leadership, planning and engineering activities changes from dealing with day to day issues to refining how the future operations runs.
As organisations make progress on their improvement journey, Improvement Leader capabilities need to remain at least one step ahead of the needs of the organisation. How do they do that?