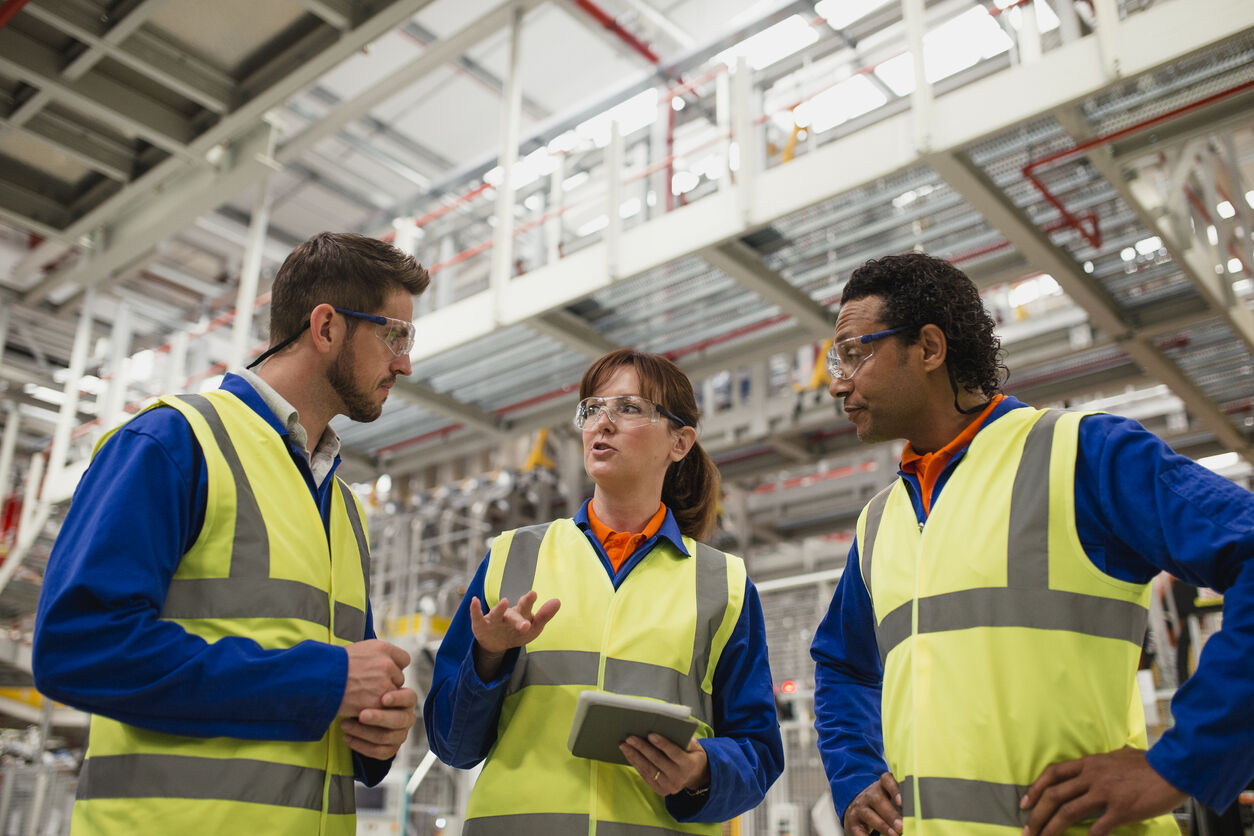
- Dates: 3 day training workshop
- Location: In Company Course
- Cost: £4500 up to 10 Delegates
- Details
- Parent Category: Courses
- Category: Ratchet Up Performance
The goal of Lean Maintenance is to stabilise and extend component life by reducing the causes of breakdowns and accelerated wear. The outcome is increased process precision, extended mean time between intervention, enhanced quality yield, higher energy efficiency and reduced manufacturing costs.
The implementation of Lean Maintenance involves:
- Analysis of assets to identify:
- Weak components, unnecessary adjustments and reasons for unplanned interventions,
- The condition of equipment and causes of accelerated wear.
- Visual standards so that the conditions for failure/accelerated deterioration can be identified at a glance and therefore do not occur,
- Weak and non value adding working methods,
- That results in:
- A prioritised list of asset refurbishment and working practices to be improved,
- Clarification of the underpinning knowledge needed to sustain Normal Conditions and recognise patterns of potential failure,
- The development of training material, training schedules, train the trainer routines and compliance assessment protocols,
- The creation of fault finding algorithms to support skill matching, notification feedback and systematic problem prevention.
- Programme Management to establish basic asset conditions, upgrade documentation, knowledge, workflow and spares management,
- The use of Lean Thinking principles to establish:
- Lean Asset Care covering preventive maintenance, inspection and servicing routines,
- Lean Execution covering standardisation, systemised workflows and engagement,
- Lean Maintenance Centre of Excellence covering skill development, performance management, focussed improvement and engagement.
This 3-day workshop leads delegates through the theory and practices of how Lean theory applies to Maintenance routines. The lessons from the practical activities are used to illustrate how following the Lean Maintenance road map can deliver:
- Effective Maintenance Execution by highlighting non value adding Maintenance routines and opportunities to enhance production and maintenance asset care workflows,
- Robust Process Stability by targeting problem hot spots, early problem detection and problem prevention routines,
- Enhanced Process Resilience by dealing with sources of accelerated wear including contamination and human error,
- Improved Flexibility of resources using standards and visual management to systemise routine tasks to make it easier to achieve core competencies,
- Reduced Manufacturing Costs by systematically resolving the causes of reactive maintenance to stabilise and extend component life.
The final session of the workshop involves the development of a bespoke Lean Maintenance route map to release maintenance resource to improve asset effectiveness. A transition from the traditional maintenance outlook of preventing downtime to one of preventing defects to deliver the full value adding potential of the maintenance function.
In addition to the above benefits, incorporating Lean Maintenance within a Lean, TPM or Six Sigma programme has been shown to increase annualised gains by as much as 50%.