Blog
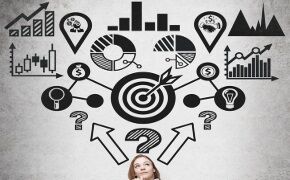
The articles below explain how to overcome common barriers to improvement and how industry leaders sustain the gains where others are not able to.
This is based on our work with well-known and award winning organisations. There is much to learn from them. If there are any topics you would like is to add, please get in touch.
For more detailed articles check out our DAK Academy website guide which contains links to videos, articles and downloads.
The Science of Learning New Skills
- Details
- Category: Blog
In Manufacturing and Process plants, the most common causes of lost performance and wasted effort are front line skill and knowledge gaps.
Most frequently this is because the way in which tasks are defined and deployed conflicts with the Science of Learning. Here is how to fix this.
Enhancing Project Management Processes
- Details
- Category: Blog
Every business needs to develop the capability to deliver projects well to respond to changes in market conditions and advances in technology.
Unfortunately, studies show that only 1/3 of organisations achieve their planned level of return on investment. Most managers and engineers have had experience of when things go wrong including troublesome new assets that take months of effort before they can be used productively.
Research into the causes of project failures indicate a number of common oversights. Find out how to avoid these, enhance project added value and speed up time to beneficial operation.
Setting the Right Priorities
- Details
- Category: Blog
When your organisation is trapped in a cycle of fix and failure it can be difficult to break out of it. Even though the definition of insanity is doing the same thing over and over again and expecting a different result, when you are in the muck and bullets it is not easy to be objective about what to do next.
In our experience, the answer is as much to do with mindset as it is with tools and techniques. In particular, it is important to avoid a mindset that focusses on the top few issues of the day because research shows that:
Spot The Problem: A Skill For Leaders To Learn
- Details
- Category: Blog
In my youth in Liverpool I remember a football edition of the Liverpool Echo (known as the football pink) which had a competition called spot the ball. The winner of the competition was the one who guessed where the ball was.
Daily Management In A Digital World
- Details
- Category: Blog
Organisations that successfully embrace the improved connectivity of digital technology at scale see a step change in performance. Where many organisations fail is by adopting a mindset that characterises the future gains in terms of one off cost savings. This is a journey not a destination. A CI journey of matching pain points with relevant digital solutions, testing and adapting to establish the new ecosystem then using that new ecosystem to deliver and lock in the gains.
Measuring Maintenance Effectiveness
- Details
- Category: Blog
Effectiveness is a measure of how well a process achieves its purpose, a measure of how often that process hits that "right first time" sweet spot. The gap between the Effectiveness achieved and 100% is a measure of the health of the process.
Although the most widely used measure of effectiveness is OEE (Overall Equipment Effectiveness), Effectiveness can be applied to improve any process including Maintenance Management.
So what?
Maintenance is most effective when engineers time is directed towards getting the most out of the asset. The table below contains the results from a food processing and packaging plant on their journey from over 80% of time spent on reactive maintenance to less than 10%.
The Power of an Improvement Glide Path
- Details
- Category: Blog
Organisations that achieve year on year improvement in OEE use it as a "Leading rather than Lagging" Indicator.
That is they use OEE analysis to clarify future improvement potential and apply relevant Focussed Improvement tactics to systematically deliver that potential.
Workplace Learning a Shortcut to Better Performance
- Details
- Category: Blog
Some organizations don't pay enough attention to people development. To them, it looks like a detour, when it is actually a shortcut to better performance. Particularly when it is considered as part of the routine.
Then it becomes workplace learning which can be used to surface and resolve the causes of waste and unplanned downtime as part of the day to day routine.
That typically deliver gains of 6 to 8 times the investment in time and resource. Something that far exceeds the Return in Investment of most capital projects.
Harvesting Gains From Digitisation
- Details
- Category: Blog
The wider use of online meetings during the lockdown shone a spotlight on the opportunities that embracing the digital world can deliver. Just as Zoom calls close the gap between the physical and digital to make collaboration easier, there are gains to be made by manufacturers who recognise the potential of digitised work routines.
Meeting The Reliability Challenge
- Details
- Category: Blog
Understanding The Nature of Unplanned Downtime
Equipment Reliability discussions often focus on component failure yet this is only part of the picture. The delivery of high levels of reliability depends on more than technical expertise. As important is the way in which the leadership conversations drive front line Operator and Maintainer mindsets and behaviours.
Compare the behaviours of two engineers responding to a failure caused by a broken chain that has stopped production.