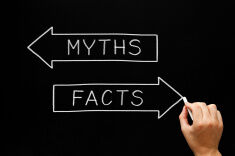
- Details
- Category: Blog
In theory prioritising issues is simple. Use a pareto to identify the asset with the most problems and work in that.
Unfortunately, it isn't as simple as that. The fault pareto analysis below showing the outputs from a shop floor data capture system, seems to indicate the main culprit to work on but this analysis isn't providing the full picture.
Firstly 5 out of the 6 items in this pareto are sensor related. There is a common cause for all of these items which isn't clear when looking at items individually
Fault |
Time |
Events |
Bottle inspection system not ready |
18:14:54 |
410 |
Bottle present sensor |
13:49:03 |
555 |
Discharge-Discharge table 1 |
12:26:30 |
401 |
Lack of caps |
6:04:24 |
544 |
Temperature sensor Fault |
5:41:15 |
269 |
Coder alarm fault |
1:24:27 |
36 |
Table 1 Pareto of Line Faults (Case Study)
The causal factors behind those 5 relate to human error and the countermeasures involve improving working methods to resolve the knowledge and skill gaps that are the causes of almost 9 out of 10 recurring problems. In short, submitting each of these to individual problem solving will not resolve the true causal factors.
In contrast, adopting the TPM centre of excellence road map will deliver lasting improvement because it views this data through the lens of improving "Effectiveness", A measure of how well did we do what we expected to do. That encourages an outlook on making things work as they are supposed to then refining how work routines are carried out so that it is easy to do right, difficult to do wrong and simple to learn.
Once in place, that releases the time to optimise process capabilities and progress towards no touch production capabilities. In this case, the priorities are set based on potential gain, not past losses.
What the Data is really saying
The above data is telling us that even in this world of smart technology the fundamentals haven't changed and that there are gaps in the fabric of management. Part of the recipe for dealing with these issues is a close collaboration between production and maintenance in Core skill areas such as:
- Proper operation,
- Conditions of use, daily deterioration checks,
- Periodic inspection,
- Trend testing,
- Rapid discovery of abnormalities, prompt and accurate reporting,
- Improving procedures and work quality.
These are part of the TPM centre of excellence Roadmap steps. Find out more