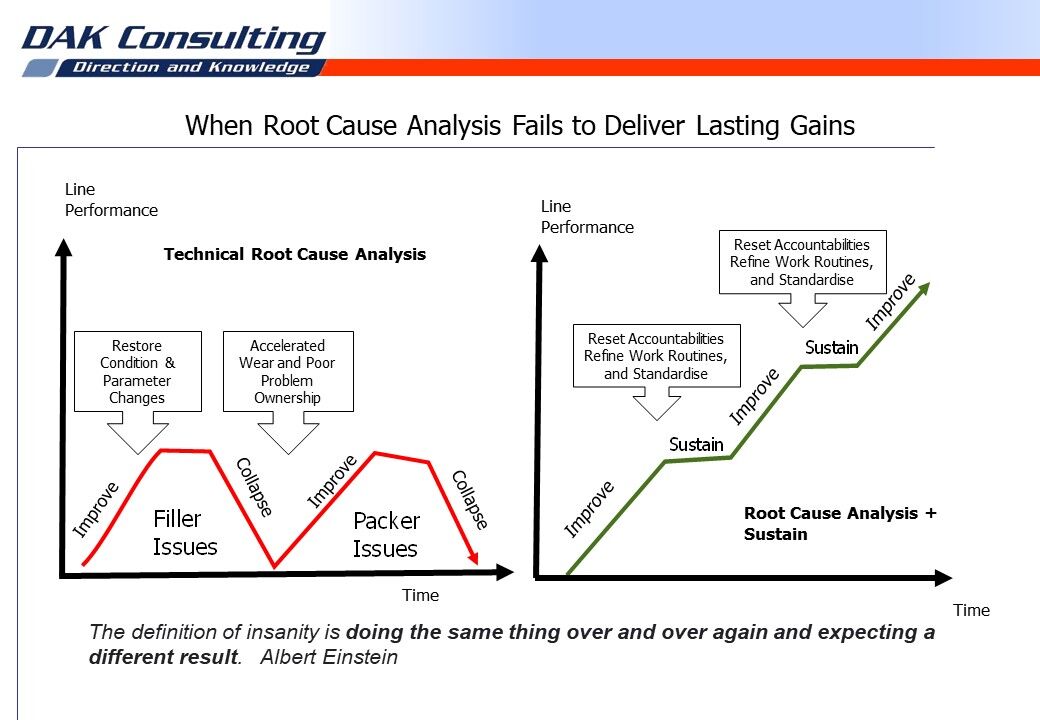
- Details
- Category: Blog
When your organisation is trapped in a cycle of fix and failure it can be difficult to break out of it. Even though the definition of insanity is doing the same thing over and over again and expecting a different result, when you are in the muck and bullets it is not easy to be objective about what to do next.
In our experience, the answer is as much to do with mindset as it is with tools and techniques. In particular, it is important to avoid a mindset that focusses on the top few issues of the day because research shows that:
- Around 40% of repetitive downtime issues are due to a lack of knowledge which leads to poor problem ownership and avoidable human error.
- Another 40% or so is due to poor equipment condition.
- So only the final 20% or so are resolved permanently by technical fixes.
That means that after a technical fix, on most occasions, there is a need to fix process weaknesses which can take more than 24 hours to resolve. Also there is a need to do that in a way that assigns problem ownership for refining work routines to those in a position to:
- Identify excess wear earlier.
- Prevent the recurrence of conditions that led to the failure.
That is a role best carried out by cross functional front line teams. An investment in time which usually returns 6 to 8 times the cost in annualised benefits. As a bonus it also increases engagement and motivation of front line personnel.
In the graphic below, the situation on the left illustrates what happens when equipment condition and technical weaknesses are dealt with but gaps in problem ownership are left alone.
The situation on the left prevails where the search for "answers that matter" is driven by a quest to solve the top issues of the day. The outcome is that actions are only triggered when something goes wrong. When the pain goes away, the pressure to improve is reduced until the next problem is revealed.
In the right hand situation the search for "answers that matter" is driven by a quest to prevent problems. Here actions are triggered until something reaches the desired result. The outcome is a proactive approach to resolving trouble spots and a creative pressure to find opportunities to improve.
The LeanTPM road map was developed to guide the transition in outlook from the left to the right hand situation by engaging all levels of the organisation with:
• Establishing basic conditions (Plus the capability to sustain that standard)
• Refining work routines so that they are easy to do right, difficult to do wrong and simple to learn
• Developing the insight to increase the precision of process control, reducing quality defects, manufacturing cost and improving customer service.
To find out more, go to "Finding Answers that Matter" in our resources section.