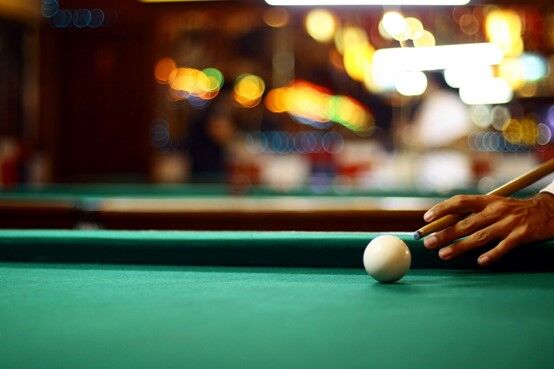
- Details
- Category: Blog
Top Snooker or Pool players continually practice the basics so that when the pressure is on, they can rely on their instincts to pull them through.
Below is a list of the equivalent basic skills for successful project delivery many of which are missing from traditional project management training such as Prince 2.
With these capabilities, stakeholders from junior team members to Project Governance roles are able to surface issues early and make decisions that secure the glide path to flawless day one operation.
These are part of the Early Equipment Management toolkit. An approach developed by leading organisations to overcome the causes of common project failures and deliver constantly high capital project Return on Investment levels.
Project Specification Skills
- Scoping the Project: Recognise that the solution will emerge over a number of steps. Mobilise a cross functional team involving customer facing, operations and technology personnel. Use the mobilisation session to brief them on the business challenge.
- Planning the Plan: Learn how to use milestone planning to set out a project road map covering actions to capture current knowledge, systematically explore options, organise resources, enhance project added value, surface and mitigate future risk.
- Managing Risk, Make sure that the programme includes tracking of Market, Financial, Operational and Volume risks. That needs to balance judgement about the future with current knowledge.
- Measuring progress: Agree in advance the completion criteria for each milestones to set out what good look like at each project phase. Use these to trap problems, capture learning, update risk probabilities and confirm readiness to proceed at each milestone. Involve those with an insight into each area so that they can feedback any concerns.
- Creating Timetables: Develop timing plans in outline for the overall project, in detail for the next 2 milestones. Leave detailed planning as late as possible to allow for changes in circumstances and improving insight.
- Engaging users: Integrate all internal and external workstream plans against the project milestones so that there is a single, realistic and achievable plan for all project workstreams.
- Working with Vendors: Formally confirm that vendor and sub contractors plans are realistic and achievable and that they are ready to proceed at each milestone.
Project Delivery/Factory Readiness Skills
- Collate tacit knowledge by documenting the current "day in the life of" cycles (start up, steady state, close down) and capturing things that go wrong, hidden losses and contributors to human error. Make these part of the specification goals and option assessment process.
- Develop commissioning plans before selecting a vendor. This will help to surface knowledge and skill gaps as well as guide vendor selection. Add detail as part of the planning process with the vendor. That will ensure that skill gaps are identified and guide the selection/development of personnel involved.
- Formally reflect on progress at each stage gate. Timetable a couple of hours to review where you against the game plan and reflect on what you need to do next. Make sure all parties prepare for that session because that will surface weaknesses and aid communication at the review session.
- Refine plans as the details become clearer. Don't delegate this to vendors, do it in house with their support. Remember, only your people know your business well enough to make this work. This level of detailed planning can only start in earnest after vendors have been selected.
- Design a glide path to flawless operation from day one with check points for tests to confirm trajectory and assure a smooth landing.
- Plan to Improve internal capabilities from day one operation. Allocate time to capture lessons learned and simplify ways of working to reduce human error and training time. Map out the first 12 months of focussed improvement activity after day 1 to optimise and bed in the new approach.
Developing Project Team Capabilities
We find that training as part of live projects is the best way to develop capabilities around these basics. That way the training process can use current project issues to develop individual and project team capabilities based on the current challenge.
As almost all career paths include work on projects, we have also developed a project skills passport for project team members, project leaders and project governance to set out what needs to be learned and provide a record of demonstrated capabilities. That way each project provides a chapter in the development of all project members.
For more information check out our article o Developing Skills to Deliver Better Projects Faster or Contact us for more details about how we can support the development of your project team as part of a live project.