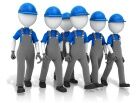
- Dates: As Required
- Location: In Company Course
- Cost: £4500 up to 10 Delegates
- Details
- Parent Category: Courses
- Category: Ratchet Up Performance
The workshop provides operational leaders and change agents across the organisation with the lean leadership skills to accelerate progress on their lean journey as part of the day to day routine.
By the end of the workshop, delegates will understand how to surface Lean wastes as well as issues and barriers to progress, apply visualisation tools that home in on key success factors, establish realistic and achievable targets and guide teams on their journey towards them.
They will know how to coach and engage direct reports with Lean improvement activities to resolve local issues that improve end to end value stream performance.
They will be able to support the development of work routines that are easy to do right, difficult to do wrong and simple to learn.